Understanding a major limitation of microscopes
The advantages of microscopy are plentiful, but they have a common limitation. The measurement field of view is small which makes it hard to measure a larger surface. That’s where an extended travel positioning system helps. Whether you are working with a digital, confocal, or structured light microscope there are considerations that need to be made to select the right positioning system to extend its field of view capabilities. These considerations can be the difference between a robust measurement process and a failed measurement result.
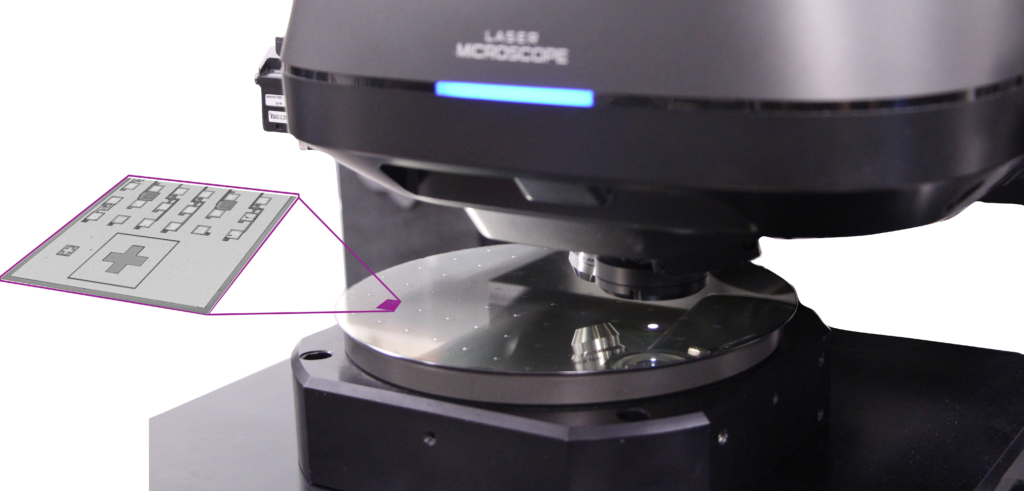
Start by figuring out what can move
The area that a microscope can measure without moving it or the sample is typically less than a few millimeters. If you want to measure a larger surface something has to move. The three options are moving the surface being measured or the microscope itself, or both.
Typically, the restrictions on how the sample can be held dictates which options are available. If you can move your part, at least in one direction, it provides the most flexibility in positioning system design and capability. If you cannot move your part the only option is to move the microscope overhead of the measurement. Although this is possible it is often the highest cost. This is due to the increased complexity of managing electrical cables and maintaining measurement area flatness.
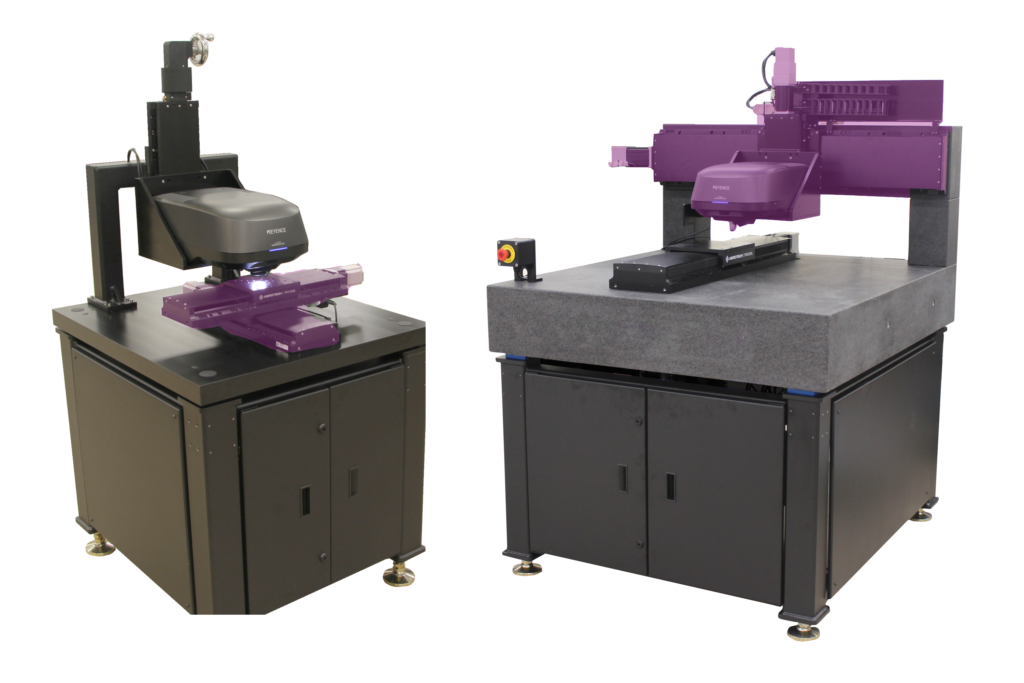
Next determine if additional stability is needed
When talking about micro and nano resolution microscopes one of the most important considerations in selecting a positioning system is measurement stability. How stable a microscopy process is depends on a variety of external factors like floor vibrations, acoustic vibrations, and vibrations caused by the positioning system itself. If any of these factors is too large the measurement results will show unwanted artifacts caused by these vibrations and will lead to false measurement readings.
Provisions should be taken to limit external disturbances. Furthermore, tailoring the provisions to the environment that the equipment will be used in will provide the best results. Ask yourself, is your floor isolated? Are other “noisy” machines operating in the same area? Is the positioning system you are looking at capable of staying put when not moving between measurement locations? The answers to these questions will tell you if an isolation system needs to be provided with the positioning equipment or not. Additionally, these answers determine if the stages selected need to be upsized to handle more disturbances.
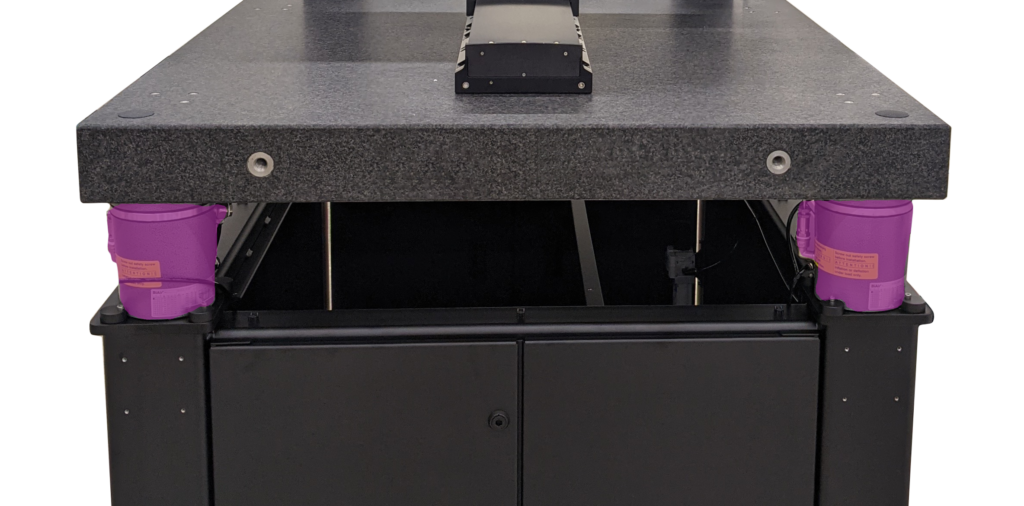
Finally, determine if more automation is best for you
Microscopy processes can be further automated with the addition of larger scale motorized positioning systems. More surfaces on larger parts are programmatically reached allowing the operator to run measurement processes autonomously. The lack of manual operator intervention increases measurement robustness and reproducibility.
What options are available? Automation systems for part loading and unloading, automatic magnification changes, and programmable measurement routines covering a range of surface positions and parameters just to name a few. These make what was an operator intensive process much more hands-off. Without this human error tighter measurement tolerances can be achieved and repeated.
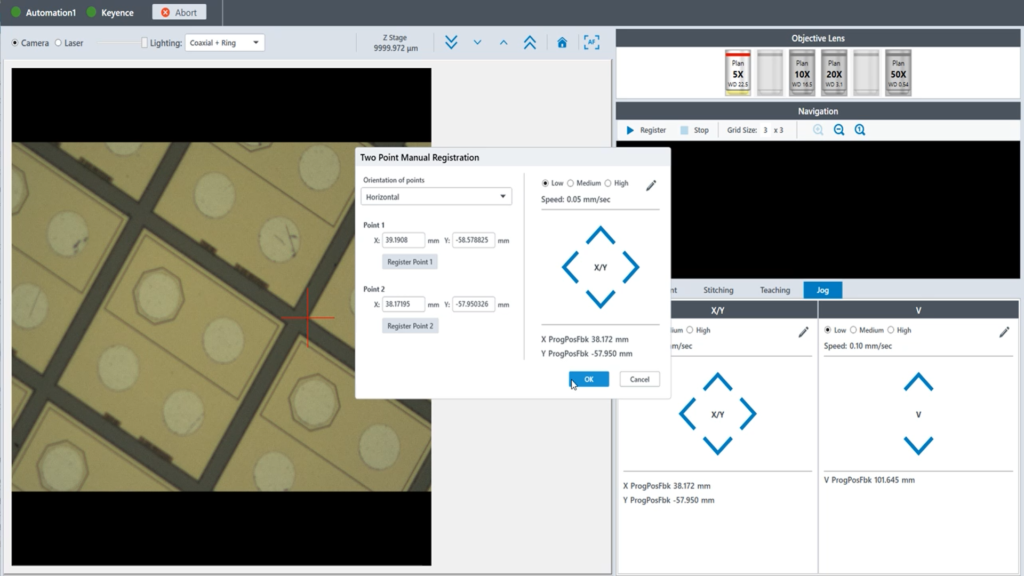
Using positioning systems to unleash your microscope
Specifying the right positioning system requires important considerations.
- Choosing what can move and what cannot
- Selecting hardware to correct for external factors such as vibration
- Pairing the right automation system to enable measurement reproducibility
If everything is specified correctly your measurement process will be more capable.
- Full part surfaces with larger areas can be measured at once
- Environmental factors will not degrade the measurement result’s integrity
- Automation will produce more reliable results with less operator interaction
For more guidance and consultation on selecting the right positioning system reach out to us.